COMPRESSED WOOD BLOCKS FOR BOX & PALLET MAKING
Reduce Labor and Equipment Costs. No additional processing required, resulting in less labor and equipment costs. Purchasing RIPS’s blocks will reduce the number of employees needed for cutting, quality inspection, and moving them through from the cut shop to the assembly line.
Accurate and Consistent dimensions, ready for assembly in automated or manual production.
Minimal swelling due to moisture and temperature changes.
RIPS’s International’s Engineered Extruded Wood block are manufactured to a variety of exact dimensions that are in demand in the market and industry specific pallets. Its’ consistent dimensions allow for less interruptions and jams during automated manufacturing setups.
RIPS’s engineered wood product. Reorientation of the wood grain structure helps to reduce splitting block failures from fork tines, provide additional resistance to nail withdraw, and helps reduce cracking of blocks due to fastener placement and shrinkage stress.
Fasteners can be driven into any face of the block without splitting and provides a comparable withdrawal resistance. The manufacturing of the engineered extruded Wood block also changes some of the mechanical properties of wood itself. The processing of the wood fiber provides a more uniform distribution of the fibers in all directions. The redistribution of these fibers strengthens certain mechanical properties of the wood. This is because solid lumber has a different mechanical value when measured in different directions.
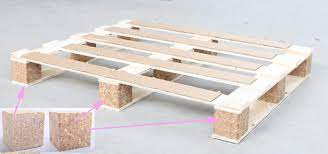
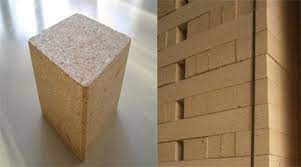
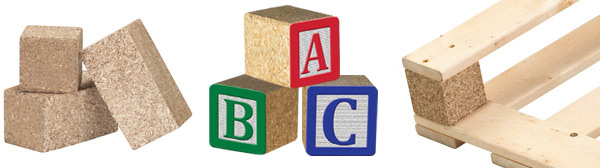
Advantages that brings it into the LimeLight
Higher Density
The blocks are composed of a mix of highly compacted softwood and hardwood fibers providing a higher overall density when compared to most solid wood. The product is also more resistance to impacts and provides better nail retention. The increased density of the Engineered Extruded Wood block provides more impact resistance to the material. In addition, the denser material provides better fastener retention. This is because fasteners’ helixes and flutes have more material to grab.
Reduces Demand for Solid Lumber
Reduce stress on facilities’ lumber supply and reduce the amount of created waste. No need to sort at the production line to try and avoid material loss with solid lumber when converting to blocks, because of wood shrinkage, warping, and twist.
Low Moisture Content
The product has no drying costs, requires no mold treatment, and causes no moisture damage to product. Moisture less than 8-10%. In addition, cracking and checking will not occur due to shrinkage from drying.
IPPC-ISPM 15 Compliance
The block is compliant with the regulation due to being a processed wood material.
Sustainable
The blocks reuse and repurpose unsuitable solid lumber and fibers into an engineered extruded wood form.
Damaged
Damaged logs, wood waste, and other wood by-products are the materials of choice for our blocks. The component materials are easily reusable for the end user as mulch, absorbents, and animal bedding
Various sizes
Various sizes are available which is Customized as per the Customer’s demand and end use requirements.